Popular Posts:
Best Alternatives to Drywall for Garage Walls
Wednesday, May 01, 2024
Cost-effective & creative alternatives to drywall for garage walls. Explore DIY options and panel materials for your garage makeover. Read more.
Comparing MDF Slatwall and PVC Slatwall: Pros and Cons
Friday, May 24, 2024
Explore the pros and cons of MDF slatwall vs. PVC slatwall. Make an informed choice for your space with this comprehensive comparison. Read more.
How to Choose the Right Garage Slatwall System for Your Space
Friday, November 08, 2024
Slatwall systems are a great way to maximize the storage space in your garage. There are some things you should consider before buying and installing one.
Latest Blog Post:
Sheetrock Vs. Drywall: What’s the Difference and Why It Matters
Friday, August 22, 2025
Wondering about the difference between Sheetrock vs. drywall? Learn how they compare, where each works best, and why Trusscore Wall&CeilingBoard is a durable, modern alternative worth considering for your home.
Tips & TricksWall&CeilingBoard
Read More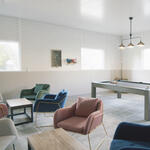
Hiring a General Contractor Checklist
Friday, August 15, 2025
Looking to hire the right contractor for your renovation? This general contractor checklist walks you through every step — plus, learn how the Trusscore Trusted Installer Program can connect you with experienced pros.
SlatWallTips & TricksWall&CeilingBoard
Read More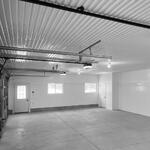
Drywall Disadvantages Every Homeowner Should Consider Before Renovating
Thursday, August 07, 2025
Discover the top drywall disadvantages, from moisture issues to ongoing maintenance, and learn why Trusscore Wall&CeilingBoard is a durable, low-maintenance alternative for your home.
Tips & TricksWall&CeilingBoard
Read More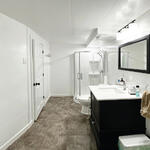
Waterproofing Bathroom Walls Without Tile: Is Trusscore the Answer?
Friday, July 18, 2025
Looking for an alternative to tile? This guide explores waterproofing bathroom walls with modern materials like Trusscore Wall&CeilingBoard — durable, low-maintenance, and 100% waterproof.
Tips & TricksWall&CeilingBoard
Read More